Seto Rx 1.499/1.56 // 1.60/1.67/1.74 Pojedynczy wizja/progresywne/niebieskie cięcie/okrągłe/płaskie bifocalne/fotochromowe soczewki
Proces produkcyjny spersonalizowanych soczewek
Indeks | 1.499 | 1,56 | 1.60 | 1.60(MR-8) | 1.67 | 1,74 |
Średnica (MM) | 55 ~ 75 | 55 ~ 75 | 55 ~ 75 | 55 ~ 75 | 55 ~ 75 | 55 ~ 75 |
Efekt wizualny | Pojedyncza wizja Płaski Roundtop Progresywny Spolaryzowane Bluecut Fotochromic | Pojedyncza wizja Płaski Okrągły Progresywny Spolaryzowane Bluecut Fotochromic | Pojedyncza wizja Spolaryzowane Bluecut Fotochromic | Pojedyncza wizja Bluecut Fotochromic | Pojedyncza wizja Spolaryzowane Niebieski cięcie Fotochromic | Pojedyncza wizja Niebieski cięcie |
Powłoka | UC/HC/HMC | HC/HMC/SHMC | HMC/SHMC | HMC/SHMC | HMC/SHMC | SHMC |
Zakres mocy (SPH) | 0,00 ~ -10,00;0,25 ~+14,00 | 0,00 ~ -30,00;0,25 ~+14,00 | 0,00 ~ -20,00;0,25 ~+10,00 | 0,00 ~ -20,00;0,25 ~+10,00 | 0,00 ~ -20,00;0,25 ~+10,00 | 0,00 ~ -20,00 |
Cyl | 0,00 ~ -6,00 | 0,00 ~ -6,00 | 0,00 ~ -6,00 | 0,00 ~ -6,00 | 0,00 ~ -6,00 | 0,00 ~ -4,00 |
Dodać | +1,00 ~+3.00 | +1,00 ~+3.00 |
Proces produkcyjny spersonalizowanych soczewek
1. Przygotowanie zamówienia:
Każda recepta na soczewkę musi być sprawdzana i obliczona indywidualnie, wówczas dane potrzebne do produkcji są generowane w postaci arkusza procesu. Arkusz procesu wraz z dwóm częściowo zakończonymi soczewkami (tj. Placki)-lewe oko i prawe oko-podniesione-podniesione- Z magazynu zostanie umieszczone w tacy. Podróż produkcyjna zaczyna się teraz: pasek przenośnika przesuwa tacę z jednej stacji do drugiej.
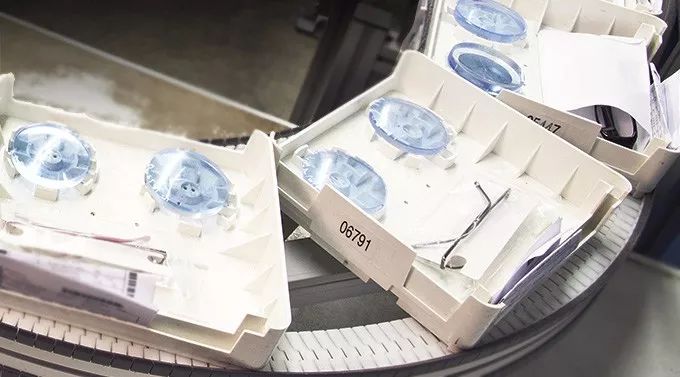
2. Blokowanie:
Aby upewnić się, że obiektyw może być mocno zaciśnięty we właściwej pozycji w maszynie, musi być zablokowany. Nałóż warstwę filmu ochronnego na wypolerowaną przednią powierzchnię półprodukcyjnej soczewki przed dołączeniem do niej z blokerem. Materiał, który dołącza do obiektywu do blokera, jest stopem metalowym o niskim tempie topnienia. Dlatego na wpół wykończona soczewka jest „przyspawana” do położenia późniejszego przetwarzania (formowanie, polerowanie i trawienie niewidzialnego logo).
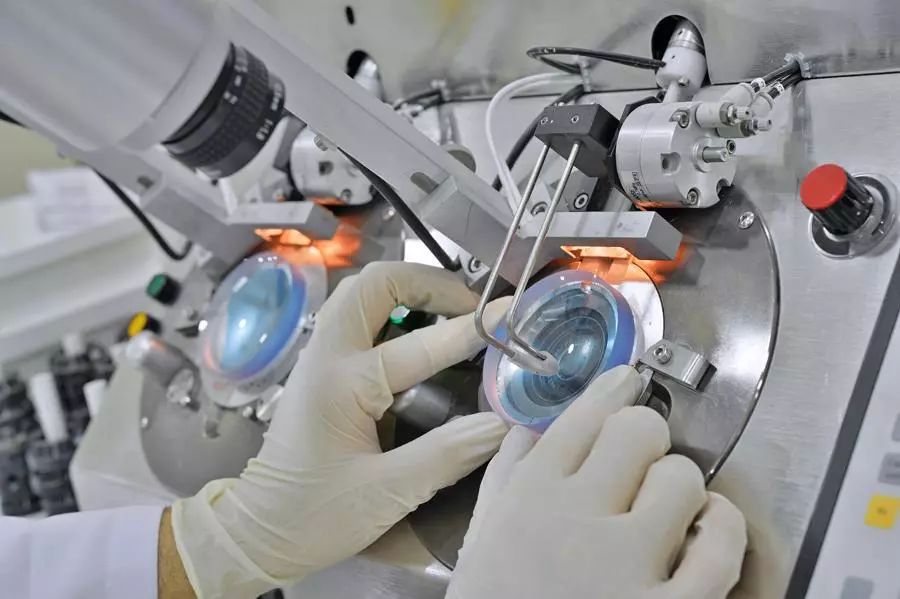
3. Generowanie
Po zakończeniu blokowania obiektyw jest uformowany do pożądanego kształtu i recepty. Przednia powierzchnia ma już korekcję mocy optycznej. Ten krok polega jedynie na wygenerowaniu konstrukcji obiektywu na receptę i parametrów recepty na tylnej powierzchni ślepej ślepej. Proces generowania obejmuje redukcję średnicy, cięcie ukośne z technikami frezowania i wykończenie naturalnego diamentu. Chropowatość powierzchni wytwarzana w procesie wykończenia jest niewielka i może być wypolerowana bezpośrednio bez wpływu na kształt lub promień soczewki.
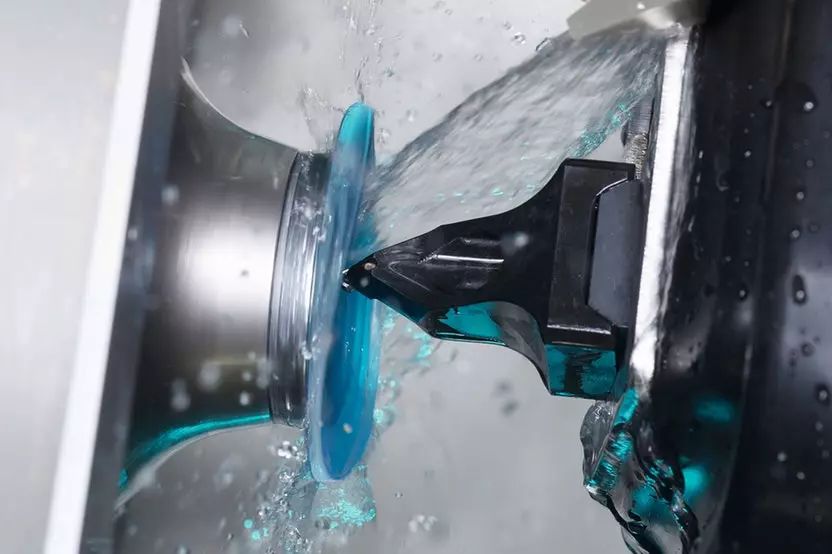
4. Polerowanie i trawienie
Po utworzeniu soczewki powierzchnia jest polerowana przez 60-90 sekund, podczas gdy właściwości optyczne pozostają niezmienione. Niektórzy producenci ukończą grawerowanie laserowe etykiety przeciwdziałania obiektywom w tym procesie.
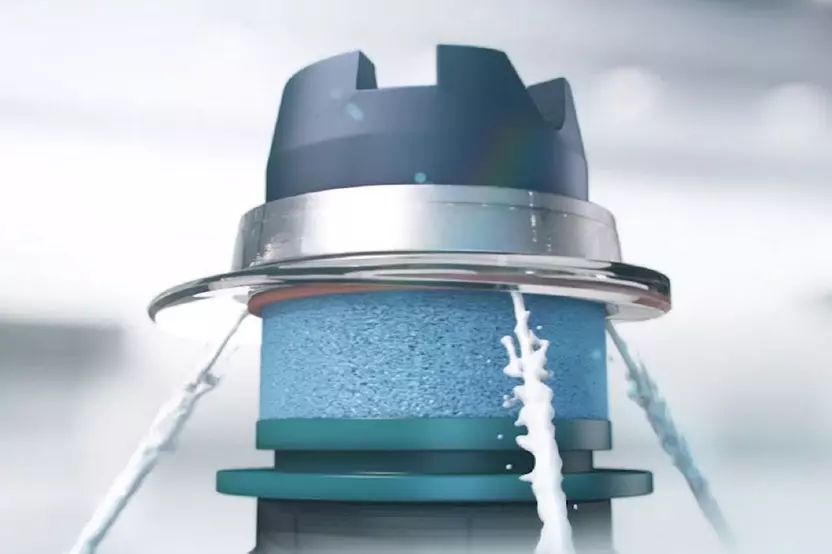
5. De-blokowanie i czyszczenie
Oddziel obiektyw od blokera i włóż bloker do gorącej wody, aby stop metalowy został całkowicie poddany recyklingowi. Obiektyw jest oczyszczany i przenoszony do następnej stacji.
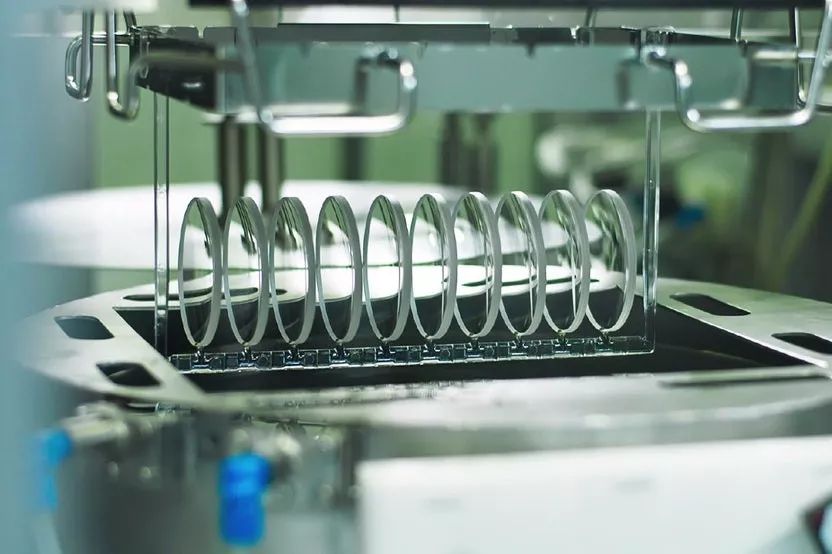
6. Tingting
Na tym etapie obiektyw RX jest zabarwiony na żądanie. Jedną z zalet soczewek żywicznych jest to, że można je przyciemnić w dowolnym pożądanym kolorze. Zastosowane barwniki są odpowiednikiem tych używanych w tekstyliach. Obiektyw jest podgrzewany i impregnowany barwnikami, umożliwiając cząsteczki barwników wnikają głęboko na powierzchnię soczewki. Po ochłodzeniu barwniki są zamknięte w obiektywach.
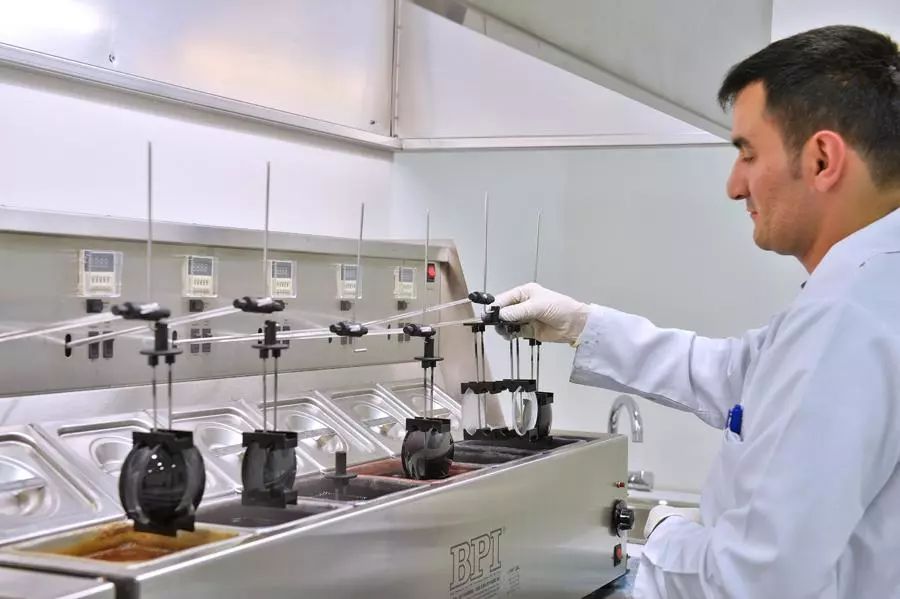
7. Powłoka
Proces powlekania soczewki RX jest taki sam jak w przypadku obiektywu zapasowego.
Powłoka powoduje, że soczewki odporne na zarysowanie, trwałe i może zmniejszyć irytujące odbicia. Najpierw soczewki Rx jest utwardzone przez zahartowane roztwory. Krok w kierunku RX dodaje się przez zastosowanie warstw antyrefleksyjnych w procesie depostingu szczepień. Ostateczna warstwa powłok Obiektyw gładka, dzięki czemu jest odporna zarówno na brud, jak i wodę, zmniejszając odbicia.
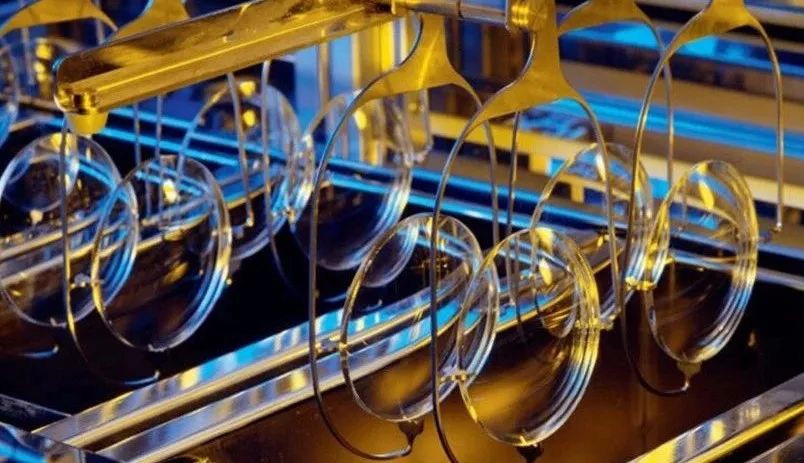
8. Zapewnienie jakości
Każdy obiektyw jest ostrożnie kontrolowany przed dostawą. Kontrola jakości obejmuje kontrolę wizualną pyłu, zarysowania, uszkodzeń, spójności kolorów powlekania itp. Następnie instrument służy do sprawdzenia, czy każdy soczewka spełnia standard, taki jak diopter, oś, grubość, konstrukcja, średnica itp.
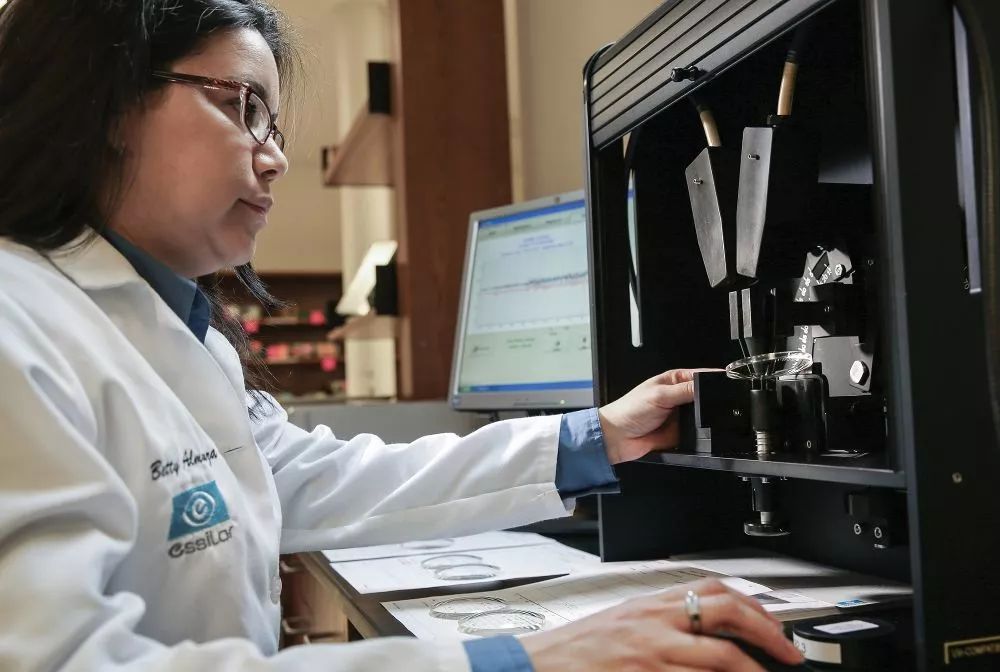
Orzecznictwo
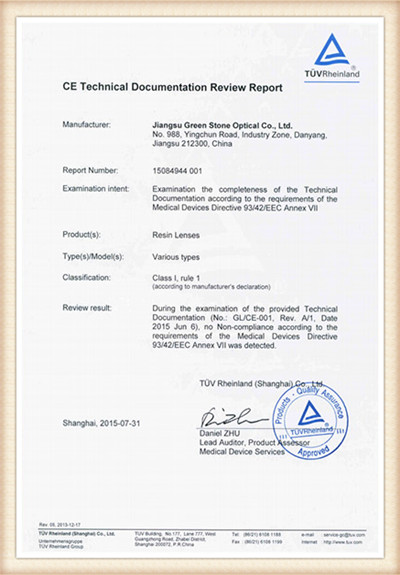
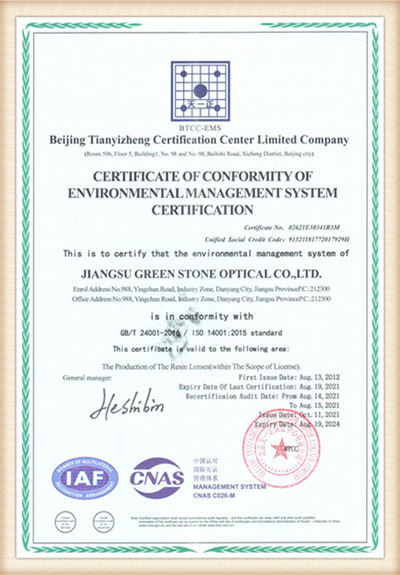
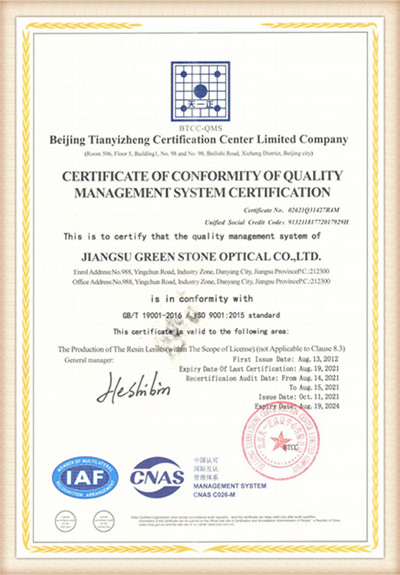
Nasza fabryka
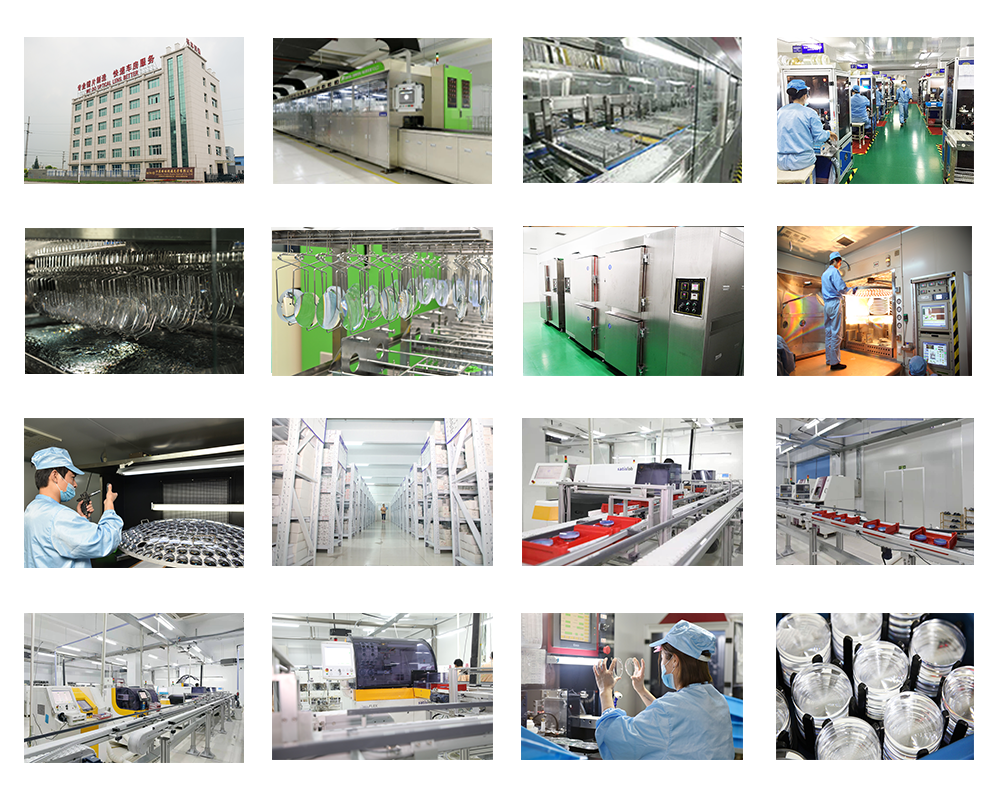